天然氣、沼氣、垃圾填埋氣和煤礦瓦斯是常見的能夠應(yīng)用于燃?xì)鈨?nèi)燃機(jī)的氣體。除此之外,有一些工業(yè)領(lǐng)域內(nèi)的廢氣含有可燃成分,例如氫氣和一氧化碳等,礦熱爐尾氣就是其中一種能進(jìn)入燃?xì)鈨?nèi)燃機(jī)發(fā)電的工業(yè)廢氣。這種廢氣雖然雜質(zhì)多、熱值低,但是經(jīng)過凈化處理以后可以進(jìn)入燃?xì)鈨?nèi)燃機(jī)發(fā)電,從而實(shí)現(xiàn)變廢為寶、節(jié)能減排,創(chuàng)造可觀的經(jīng)濟(jì)效益。
Natural gas, biogas, landfill gas, and coal mine gas are common gases that can be applied to gas internal combustion engines. In addition, there are some industrial waste gases that contain combustible components, such as hydrogen and carbon monoxide. The tail gas of the submerged arc furnace is one of the industrial waste gases that can enter the gas internal combustion engine for power generation. Although this type of exhaust gas has many impurities and low calorific value, after purification treatment, it can enter the gas internal combustion engine for power generation, thereby realizing the transformation of waste into treasure, energy conservation and emission reduction, and creating considerable economic benefits.
礦熱爐又稱電弧電爐或電阻電爐。它主要用于還原冶煉礦石,碳質(zhì)還原劑及溶劑等原料,主要生產(chǎn)硅鐵,錳鐵,鉻鐵、鎢鐵、硅錳合金等鐵合金。礦熱爐主要分為半密閉和密閉爐兩種類型,其中密閉爐產(chǎn)生的尾氣含有的可燃成分較多,能夠用于燃?xì)鈨?nèi)燃機(jī)發(fā)電。
Mineral arc furnace, also known as electric arc furnace or resistance furnace. It is mainly used for reducing smelting ores, carbon reducing agents, solvents and other raw materials, and mainly produces ferroalloys such as ferrosilicon, ferromanganese, ferrochromium, ferrotungsten, and silicomanganese alloys. Mineral heat furnaces are mainly divided into two types: semi enclosed and enclosed furnaces. The exhaust gas generated by enclosed furnaces contains more combustible components and can be used for gas internal combustion engine power generation.
Figure 1 Production and Utilization Process of Tail Gas from a Mine Heating Furnace
在礦熱爐生產(chǎn)鐵合金的過程中產(chǎn)生的尾氣(Furnace off gas,簡稱FOF)主要成分為CO,以及少量的 H2、 CO2等。其中一氧化碳(CO)氣體是由于還原劑中存在碳而形成的,如果還原劑中含有揮發(fā)性碳?xì)浠衔铮瑒t會(huì)形成氫氣(H2)。過去,礦熱爐尾氣通常是直接燃燒后排放,而現(xiàn)在則可以通過高效的燃?xì)鈨?nèi)燃機(jī)發(fā)電,同時(shí)利用高溫?zé)煔獾臒崮?,使能源得到高效充分的利用?/div>
The exhaust gas (FOF) generated during the production of ferroalloys in a submerged arc furnace is mainly composed of CO, as well as a small amount of H2, CO2, etc. Carbon monoxide (CO) gas is formed due to the presence of carbon in the reducing agent. If the reducing agent contains volatile hydrocarbons, hydrogen gas (H2) will be formed. In the past, the exhaust gas from submerged arc furnaces was usually discharged after direct combustion. However, now it can be generated through efficient gas internal combustion engines, while utilizing the heat energy of high-temperature flue gas to efficiently and fully utilize energy.
的熱值通常只有天然氣熱值的1/3左右,也就是說相比于同級輸出功率的天然氣機(jī)型,F(xiàn)OF發(fā)電機(jī)組的進(jìn)氣量需要增大3倍以上。FOF的抗爆性與天然氣也有顯著區(qū)別,其甲烷指數(shù)(Methane Number,簡稱MN)只有天然氣的大約60%左右,這意味著這種氣體在內(nèi)燃機(jī)氣缸里面更容易發(fā)生爆震。所以,燃?xì)獍l(fā)電機(jī)組需要通過傳感器監(jiān)測爆震的發(fā)生以調(diào)整機(jī)組的運(yùn)行狀態(tài)。
The calorific value of FOF power generation units is usually only about one-third of that of natural gas, which means that compared to natural gas models with the same level of output power, the intake volume of FOF power generation units needs to be increased by more than three times. The anti knock performance of FOF is also significantly different from that of natural gas, with its Methane Number (MN) only about 60% of that of natural gas, which means that this gas is more prone to detonation in internal combustion engine cylinders. Therefore, gas generator units need to monitor the occurrence of detonation through sensors to adjust the operating status of the unit.
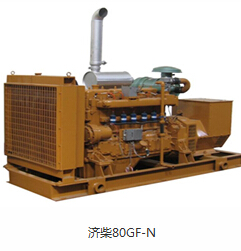
另一方面,F(xiàn)OF燃燒時(shí)的層流火焰速度(Laminar Flame Speed,簡稱LFS)卻比天然氣快許多,這和氣體里面氫氣的含量比例有關(guān)。層流火焰速度是在層流前沿發(fā)生氧化反應(yīng)的速度, 即未燃燒的混合氣與火焰前沿之間的相對速度。根據(jù)麻省理工學(xué)院的研究資料,在當(dāng)量比(Equivalence Ratio)為2時(shí),5% H2和95% CO組成的混合氣的LFS約為50cm/s,而 50% H2和50% CO組成的混合氣的LFS可到160cm/s。鑒于FOF特殊的燃燒特性,燃?xì)鈨?nèi)燃機(jī)的進(jìn)氣系統(tǒng)和控制參數(shù)都需要特殊設(shè)計(jì)以適應(yīng)其特性,同時(shí)還必須滿足NOx的排放要求。
On the other hand, the laminar flame speed (LFS) during FOF combustion is much faster than natural gas, which is related to the proportion of hydrogen content in the gas. The laminar flame velocity is the rate at which oxidation reactions occur at the front of the laminar flow, that is, the relative velocity between the unburned mixture and the flame front. According to research data from the Massachusetts Institute of Technology, when the equivalence ratio is 2, the LFS of a mixture of 5% H2 and 95% CO is about 50cm/s, while the LFS of a mixture of 50% H2 and 50% CO can reach 160cm/s. Given the unique combustion characteristics of FOF, the intake system and control parameters of gas internal combustion engines require special design to adapt to their characteristics, while also meeting the NOx emission requirements.
顏巴赫的 DIA.NE XT4系統(tǒng)在氣體質(zhì)量波動(dòng)時(shí)自動(dòng)調(diào)整設(shè)置,因此能夠適應(yīng)復(fù)雜的運(yùn)行情況。同時(shí),顏巴赫的LEANOX稀薄燃燒控制技術(shù)能夠?qū)崟r(shí)控制氮氧化物NOx的排放,確保始終滿足嚴(yán)苛的環(huán)保要求,使機(jī)組排氣出口NOx達(dá)到250-500mg/Nm3(@5% O2),并且無需SCR等復(fù)雜的尾氣后處理裝置。新的顏巴赫資產(chǎn)管理系統(tǒng)myPlant則能實(shí)時(shí)監(jiān)測、控制和預(yù)測機(jī)組的運(yùn)行狀態(tài),并能提供前瞻性的維護(hù)保養(yǎng)建議。
Yanbach's advanced DIA. NE XT4 system automatically adjusts settings when gas quality fluctuates, thus being able to adapt to complex operating conditions. At the same time, Yanbach's LEANOX lean combustion control technology can control the emission of nitrogen oxide NOx in real-time, ensuring that strict environmental requirements are always met, so that the NOx at the exhaust outlet of the unit can reach 250-500mg/Nm3 (@ 5% O2), and there is no need for complex tail gas post-treatment devices such as SCR. The new Yanbach asset management system myPlant can monitor, control, and predict the operating status of the unit in real-time, and provide forward-looking maintenance recommendations.
燃?xì)鈨?nèi)燃機(jī)對氣體的雜質(zhì)含量要求
Requirements for impurity content of gas in gas internal combustion engines
尾氣的成分和氣量與爐子的運(yùn)行參數(shù)有關(guān),并受到原料質(zhì)量、爐子控制和運(yùn)行狀態(tài)等因素的影響,所以通常會(huì)連續(xù)變化。采用氣柜來減少氣體熱值和壓力的波動(dòng),對于燃?xì)鈨?nèi)燃機(jī)發(fā)電非常重要。在爐子供氣中斷時(shí),氣柜還可以起到緩沖的作用。
The composition and gas volume of exhaust gas are related to the operating parameters of the furnace, and are influenced by factors such as raw material quality, furnace control, and operating status, so they usually change continuously. The use of gas cabinets to reduce fluctuations in gas calorific value and pressure is very important for gas internal combustion engine power generation. When the gas supply to the furnace is interrupted, the gas holder can also serve as a buffer.
進(jìn)入內(nèi)燃機(jī)前的FOF需要進(jìn)行預(yù)處理,以滿足氣體質(zhì)量要求。通常需要去除粉塵,以及多余的水分,還有焦油、硫及其他有害雜質(zhì)等。硫、氨等成分的含量要求與燃?xì)獾臒嶂迪嚓P(guān),須根據(jù)實(shí)際熱值確定上限值。下表是顏巴赫燃?xì)鈨?nèi)燃機(jī)對氣體的一般質(zhì)量要求。
The FOF before entering the internal combustion engine requires pre-treatment to meet the gas quality requirements. Usually, it is necessary to remove dust, excess water, tar, sulfur, and other harmful impurities. The content requirements of components such as sulfur and ammonia are related to the calorific value of the gas, and the upper limit value must be determined based on the actual calorific value. The following table shows the general quality requirements for gases in Yanbach gas internal combustion engines.
南非鈦鐵礦冶煉廠礦熱爐尾氣發(fā)電項(xiàng)目
South African Ilmenite Smelter Mine Furnace Tail Gas Power Generation Project
南非大的一家鈦鐵礦冶煉工廠于2012年采用了8臺顏巴赫J(rèn)620燃?xì)獍l(fā)電機(jī)組,每臺功率1,698 kW,總?cè)萘?3.6 MW。所發(fā)出的電力并入公司11 kV內(nèi)網(wǎng),用于滿足工廠部分電能需求。
A large titanium iron ore smelting plant in South Africa adopted 8 Yanbach J620 gas generator units in 2012, each with a power of 1698 kW and a total capacity of 13.6 MW. The electricity generated is integrated into the company's 11 kV internal network to meet some of the power needs of the factory.
工廠內(nèi)有兩個(gè)封閉的直流電弧爐,產(chǎn)生尾氣主要成分為73% CO, 14.5% H2,以及少量CO2等。據(jù)測算,該項(xiàng)目平均每年大約可以減少84,432 噸二氧化碳排放,是聯(lián)合國清潔發(fā)展機(jī)制CDM注冊項(xiàng)目。
There are two enclosed DC arc furnaces in the factory, which produce tail gas mainly composed of 73% CO, 14.5% H2, and a small amount of CO2. According to calculations, the project can reduce carbon dioxide emissions by approximately 84432 tons per year on average, making it a registered CDM project under the United Nations Clean Development Mechanism.
挪威錳鐵合金礦熱爐尾氣發(fā)電項(xiàng)目
Norwegian manganese iron alloy submerged arc furnace tail gas power generation project
北歐大的錳鐵合金生產(chǎn)商采用了1臺顏巴赫J(rèn)620燃?xì)獍l(fā)電機(jī)組用于礦熱爐尾氣發(fā)電 ,輸出功率 1.5MW。尾氣的主要成分為65% CO, 5% H2, 8% CO2等,低位熱值(LHV)大約2.8 kWh/Nm3。項(xiàng)目于2020年調(diào)試完成并投入商業(yè)運(yùn)行。
Nordic manganese iron alloy manufacturers have adopted one Yanbach J620 gas generator unit for generating tail gas from submerged arc furnaces, with an output power of 1.5MW. The main components of exhaust gas are 65% CO, 5% H2, 8% CO2, etc., with a low calorific value (LHV) of approximately 2.8 kWh/Nm3. The project was commissioned and completed in 2020 and put into commercial operation.
通過回收礦熱爐尾氣用于熱電聯(lián)供系統(tǒng)(CHP),減少工廠對來自電網(wǎng)的電力需求,節(jié)省了電能成本,而系統(tǒng)產(chǎn)生的高溫?zé)煔鈩t用于冶煉前對礦石進(jìn)行干燥。該工廠的目標(biāo)是通過CHP的使用將工廠的能源效率提升40%。同時(shí),該項(xiàng)目也因其在環(huán)境保護(hù)和節(jié)能減排方面的突出貢獻(xiàn),獲得了挪威政府的大力支持。
By recycling the exhaust gas from the ore furnace for the combined heat and power supply system (CHP), the factory's demand for electricity from the power grid is reduced, saving electricity costs. The high-temperature flue gas generated by the system is used to dry the ore before smelting. The goal of the factory is to increase its energy efficiency by 40% through the use of CHP. At the same time, the project has also received strong support from the Norwegian government due to its outstanding contributions in environmental protection and energy conservation and emission reduction.
礦熱爐尾氣的發(fā)電應(yīng)用充分利用了廢氣,將其轉(zhuǎn)化為電能和熱能,是冶煉行業(yè)節(jié)能減排和循環(huán)經(jīng)濟(jì)的榜樣。通過對廢氣的利用變廢為寶,在改善環(huán)保排放的同時(shí)創(chuàng)造新的價(jià)值,節(jié)約了企業(yè)的運(yùn)營成本。顏巴赫在該領(lǐng)域擁有豐富的經(jīng)驗(yàn),其發(fā)電機(jī)組產(chǎn)品單機(jī)功率大,發(fā)電效率高,調(diào)試周期短,可靠性好,能夠有效幫助用戶獲得可觀的收益和顯著的碳減排效果。在我國“雙碳”戰(zhàn)略目標(biāo)的大背景下,隨著對冶金行業(yè)環(huán)保要求的不斷提高,礦熱爐尾氣的高效利用將擁有廣闊的發(fā)展前景。
The power generation application of the tail gas of the submerged arc furnace fully utilizes the exhaust gas, converting it into electrical and thermal energy, and is an example of energy conservation, emission reduction, and circular economy in the smelting industry. By utilizing exhaust gas to turn waste into treasure, we can improve environmental emissions while creating new value and saving operating costs for enterprises. Yan Bach has rich experience in this field. His generator set products have high single unit power, high power generation efficiency, short debugging cycle, and good reliability, which can effectively help users achieve considerable profits and significant carbon reduction effects. Against the backdrop of China's "dual carbon" strategic goal, with the continuous improvement of environmental protection requirements for the metallurgical industry, the efficient utilization of tail gas from submerged arc furnaces will have broad development prospects.
The exciting content of this article is provided by the knowledge of alloy exhaust gas generator sets. There are also many exciting content on this website, and you can click to enter more content: http://m.dgtmcnc.com We have dedicated customer service to answer your questions